A range of issues plagues the automotive industry: from CO2 emissions to be reduced, to the increasing costs of purchasing raw materials, to the problem of disposing of exhausted batteries.
A solution already researched by many manufacturers is the implementation of circular economy models.
The European directive 2000/53 has already made it clear for some time that 95% of the car's weight is made up of recoverable materials. However, the concept of recycling raw materials generally applied today can be described as "downcycling": obtaining recycled components with a lower use value than the original one. For example, car parts are usually recovered not in industrial processes but from junkyards, which generate very low-value metal alloys.
On the other hand, there is upcycling, which is fundamental in modern circular economy models. If we want to create closed production cycles, the recovery components must have the same value – or not much lower – than the original ones. In this way, companies will be able to decrease the purchase volumes of raw materials, with both economic and environmental benefits.
In other words, where recycling aims to cause less harm to the environment while maintaining linear production models, upcycling aims for closed production chains, removing (or greatly decreasing) the need for raw materials.
How does upcycling work?
The central concept of upcycling is the realization that waste parts aren't a problem to be solved but an opportunity to be seized.
First of all, to increase the quality of waste products, a revolution in cars design is necessary: simplifying the layout and considering an end of life from the very beginning.
Change is also necessary for the production process: in factories, disassembly lines should be inserted to industrialize and speed up the disassembly operations.
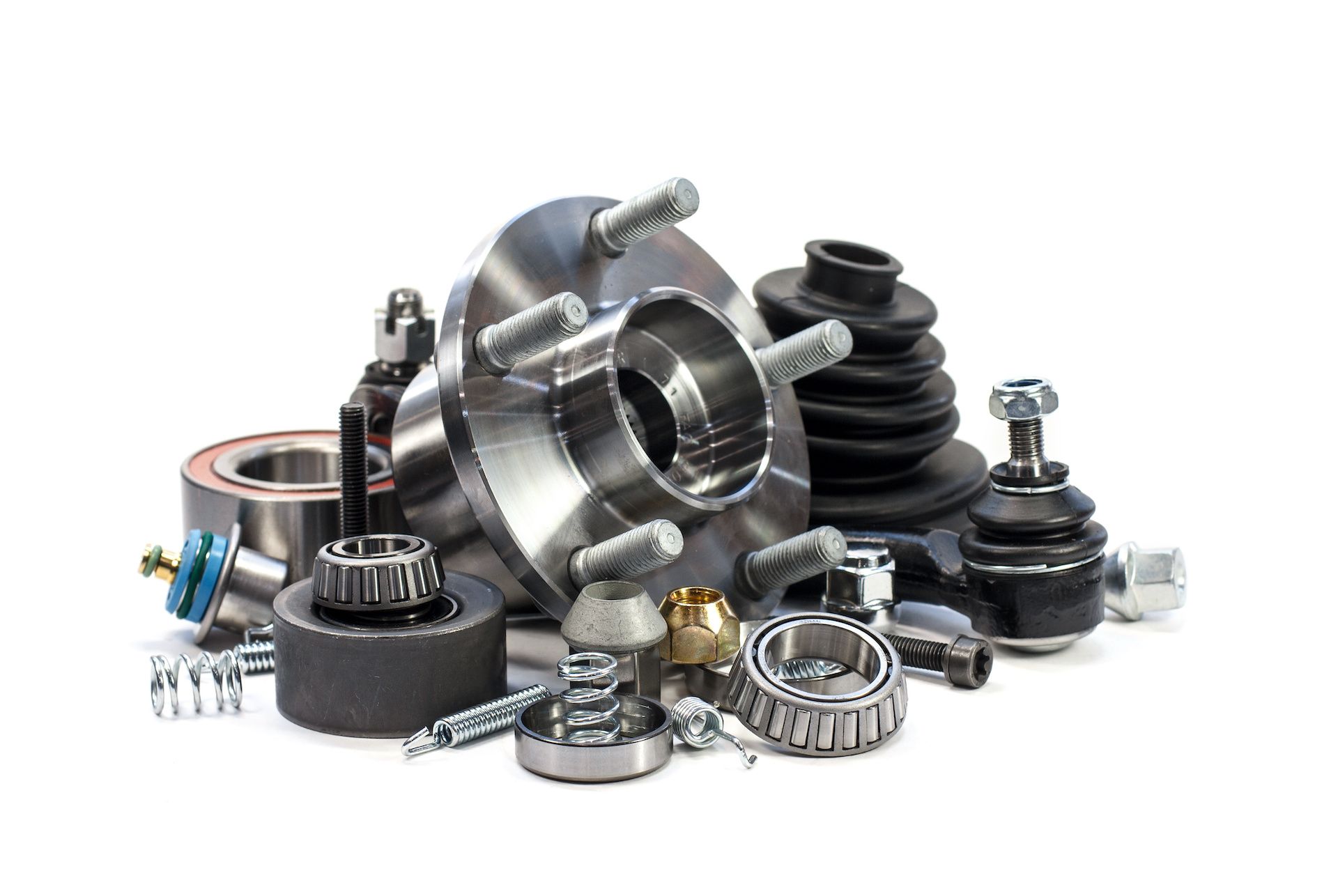
To make the disassembly effective it will be necessary to better know the condition of engines and other components. The era of big data solves this problem through the smart sensorization of cars.
Product-as-a-service business models will be very useful in this sense: selling the car not as a physical object but as a high-quality service. This makes it possible for manufacturers to have greater control over matter and technology. There will also be another level of incentive to extend the life of the components since the car will remain the manufacturer's property. There are several advantages: there'll be a more service-like experience for the customer, while the environment enjoys fewer cars and lower emissions.
In a future where raw materials will be increasingly rare and expensive, recovery as "upcycling" will become the order of the day.
But circular economy models are not just the future
A pioneer in reducing environmental impact is none other than Henry Ford, the inventor of the assembly line. It's said that shortly before his death, he was working on the first car disassembly factory.
Following this line of thinking, in 1937, Henry Ford introduced the world to the Soybean Car, a prototype car made of soybeans, wheat, and corn. A model that, in terms of construction weight and simplicity, far surpassed the metal cars of the time. However, the project vanished due to the hemp ban as the vehicle was supposed to run on hemp fuel.
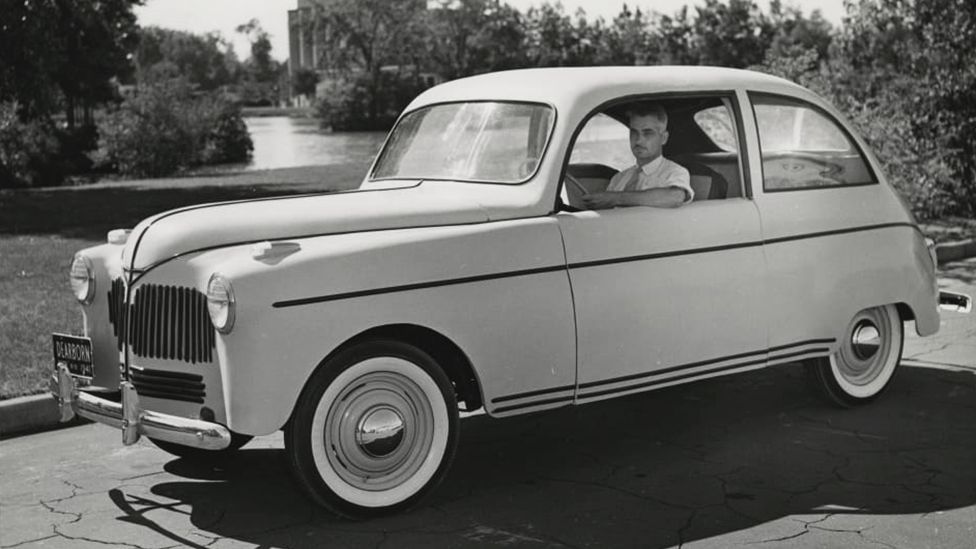
Taking a step forward to 2012, we find the first car remanufacturing factory managed by Renault at the Choisy-le-Roi plant. Here, engines, mechanical gearboxes, turbos, injection pumps, and discarded cylinder heads kits are disassembled. Some of these components, through a clever design, can be reused in new models' production. Others are remanufactured as replacement parts at a reduced price.
Figures indicate that Renault has reduced electricity consumption by around 80 percent and waste by over 70 percent.
Renault will also open a Re-Factory in Flins in 2024, the first automotive factory entirely dedicated to the circular economy. The objectives are life-extension, green energy management and in particular of electric cars, and high-quality recycling.
Rapid innovation in tire reuse
Let's stay in France because a major investor in this field is tire giant Michelin. They've been supplying tires as a product-as-a-service for years. Thanks to an increased ability to keep track, used tires are rebuilt while maintaining 90% of the performance of the new tires. Instead, when the tire can no longer be repaired, it becomes high-quality regenerated rubber or ethanol, both of which can be reused in the production cycle.
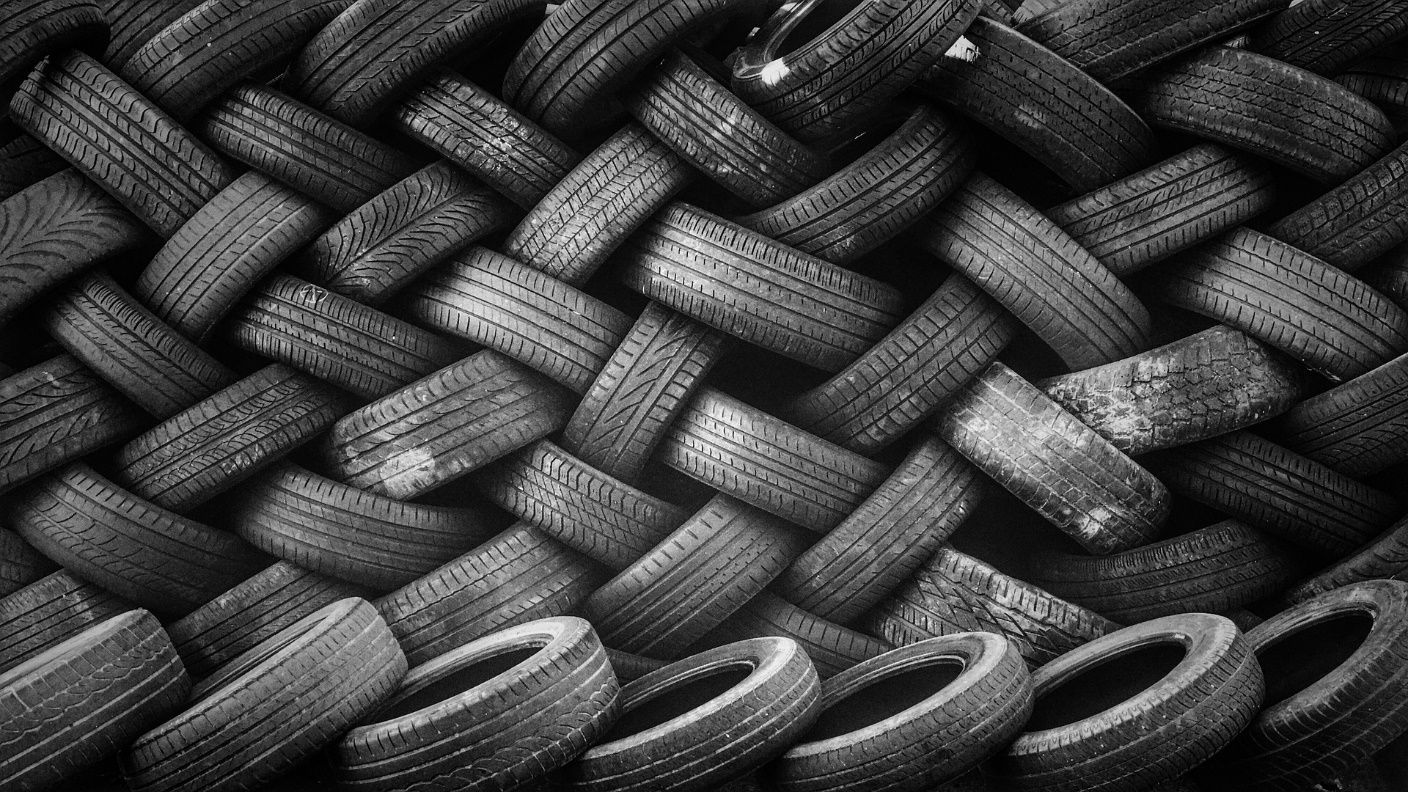
Currently, Michelin, in partnership with Carbios, is trying to make the first 100% sustainable tires. The innovative enzymatic recycling technology they've developed makes it possible to obtain rubbers from recycled PET from bottles, clothing fibers, etc…
This technology uses an enzyme capable of totally depolymerizing PET, which can be reused as a secondary raw material with the same properties as virgin material.
The process has been validated and intends to produce the first tires exclusivly from recycled materials by 2050.
Closing cycles requires revolutionary ideas
The journey towards advanced upcycling in the automotive industry comes to Germany. A manufacturer investing heavily in the circular economy is Audi, which since 2019 has started a series of projects to close its production cycles.
Audi has already activated the "Aluminum Closed Loop" project to reuse aluminum, a material of great impact in its processing. Recycled aluminum maintaining the same quality as virgin material is used for the production of components, resulting in a 95% reduction in energy consumption.
Another project aims to produce car interiors using PET recycled from bottles. This requires a complex production process, where the bottles are crushed into granules which in turn is used to create polyester threads and plastic yarns. The interior of the new A3 Sportback is already 89 percent made from recycled materials with an identical texture and appearance to the original.
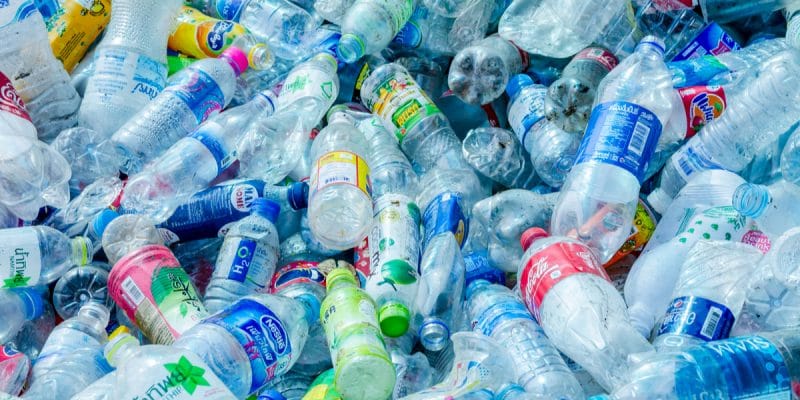
A particularly innovative project was recently launched in partnership with the Karlsruhe Institute of Technology. Many plastics are not recoverable with current processes, especially those made with a mix of polymeric raw materials. The recovery of these waste components is being studied through chemical recycling. This process allows obtaining pyrolysis oil to be used in the production cycle of components instead of petroleum products, with similar qualities.
And of course – the electric car itself
The electric motor is a simpler construction than the internal combustion engine: it has fewer components and fewer joints. Therefore, besides being more efficient and less polluting, it's also more suitable for remanufacturing since it's easier to disassemble.
Further reconfirmation that the future belongs to the electric.
However, effective solutions for the recovery of heavy metals (lithium) from batteries have not yet been found. It's estimated that less than 5% of these materials are recovered today, moreover through high-impact processes. Research is fervent in this field from many manufacturers, including Audi and Renault.
A particularly interesting project is underway at Coventry University, where a research team led by Prof. Farnaud is investigating the recovery of lithium through Bioleaching.
It's a natural process, which uses bacterial species (eg Acidithiobacillus ferrooxidans), which naturally "feed," oxidize and extract heavy metals as part of their metabolism. They are obtained in crops at 37 °C without the need for high temperatures or toxic chemicals, therefore with very low emissions.
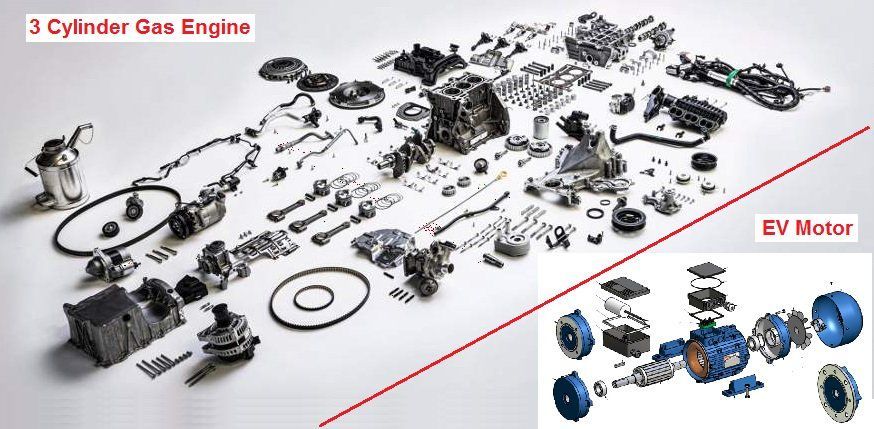
The research is ongoing and represents the last step before the surge that's bound to happen anyway: it's estimated that by 2025 electric cars will cost favorably when compared to their combustion-powered equivalents.