30 percent of humanity still lacks safe access to drinking water and the UN fears that the figure will be even higher in 2030 if nothing is done. One thing that could help to solve the problem, is if there was a efficient and cheap way of cleaning and reuse dirty water.
This is exactly what a research team from KTH and Politecnico di Torino in Italy are working on. They have, according to a press release, developed an environmentally friendly method for removing heavy metals, dyes and other contaminants from water. The method is based on dirty water being allowed to flow through a special kind of hydrogel that catches all pollutants.
“The total amount of water available on earth will not change over time, but the need for water does. This hydrogel, which consists of lignocellulose, is a promising, durable material to secure access to clean water” , says Minna Hakkarainen, professor and chef at the Department of Polymer Technology at KTH and one of the researchers behind the hydrogel, in a press release.
The hydrogel consists of lignocellulose and carbonized biomass. Lignocellulose can be made from different types of plant materials such as wood pulp or residues from cotton cultivation. As plant mass is the most common biomass on earth, it is both cheap and easy to obtain.
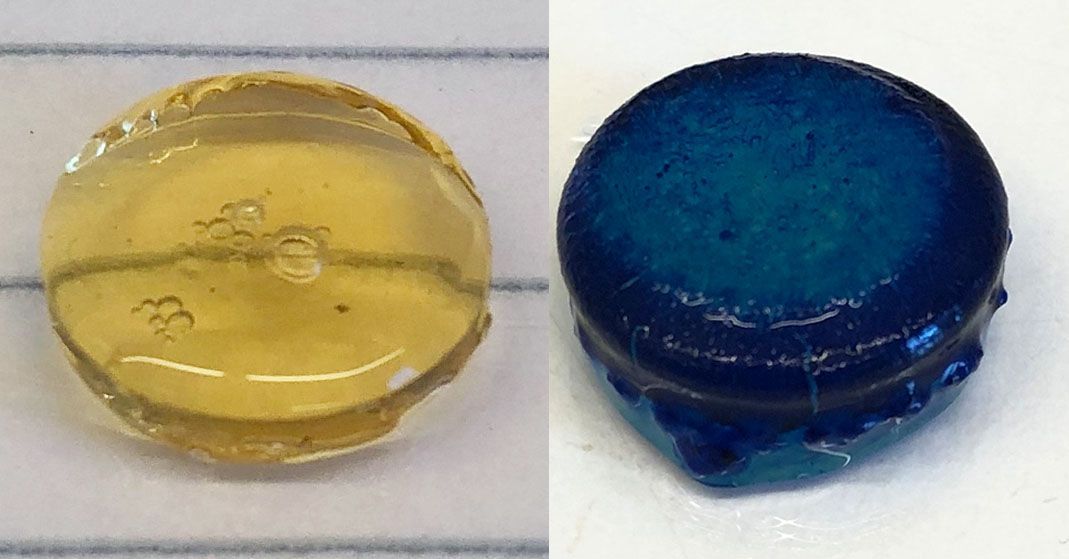
But the hydrogel also needs another component to be able to purify water. Here, the researchers have tested a new way. There are similar hydrogels and they often use graphene oxide. It is a material that is very good at capturing pollutants, but it has environmental problems. The production requires chemicals that are not good for the environment and high temperatures are needed, which consumes a lot of energy.
“Graphene oxide is an excellent adsorbent, but the production of the substance is tough for the environment. We have instead chosen to use bio-based material and a process that has a significantly lower impact on the environment in the production” says Minna Hakkarainen.
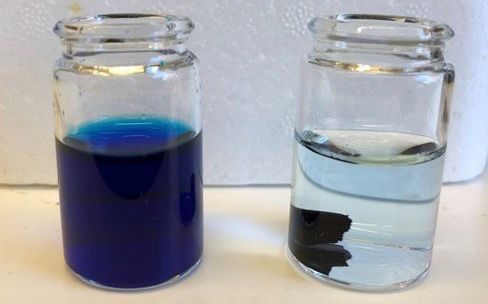
What the researchers have done is that they have converted lignosulfonate, a by-product of wood pulp, into carbon flakes by heating it in water in a microwave oven.
Instead of a process that normally requires energy-consuming ovens that need to generate temperatures of 1,300 degrees, the 240 degrees that a microwave oven can reach are sufficient. After heating lignosulfonate mixed with water in the microwave, the researchers get small pieces of carbon 10 to 80 nanometers in diameter.
These carbon pieces are mixed with the cellulose rubber. The final step is to put the mixture under UV light, it then becomes a hydrogel.
” This is a simple, sustainable solution. It works just as well, if not better, than similar hydrogel-based purification techniques used today” says Minna Hakkarainen.
Image: Pixabay / Baudolino